アルミプレートのネジ切り・タップ加工
アルミプレートは、その軽量性、優れた加工性、そして多様な合金種による特性の幅広さから、航空宇宙部品、半導体製造装置、精密機器、さらには建築材料に至るまで、あらゆる産業分野で不可欠な素材となっています。そのアルミプレート加工において、部品の締結や機能付与に欠かせないのが「ネジ切り・タップ加工」です。
しかし、「たかがネジ穴」と侮ってはいけません。材質の選定ミス、不適切な下穴径、工具選択の誤り、最適でない切削条件は、加工不良、強度不足、タップ折れといった致命的なトラブルを引き起こし、製品の品質低下や納期遅延、コスト増大に直結します。
この記事では、材質選定から下穴加工、最適なタップ工具の選び方、切削条件の最適化、強度確保策、タップ折れ防止策、NC加工における注意点、そして最後の仕上げに至るまで、アルミプレート加工の品質と効率を最大限に高めるための実践的なノウハウを網羅的にお届けします。
1.材質選定とその影響
アルミプレートにネジ切り・タップ加工を行う際、最初のステップであり最も重要なのが、適切なアルミニウム合金の選定です。合金の種類によって、強度、切削性、耐食性などが大きく異なり、これらが加工精度や製品の耐久性に直接影響します。
代表的なアルミニウム合金とその特性
合金種類 | 特徴 | 主な用途 | プレート加工時の注意点 |
A2017 (ジュラルミン) | 高強度、良好な切削性。 | 航空機部品、精密機器部品 | 耐食性が劣るため、使用環境に応じて陽極酸化処理(アルマイト)などの表面処理が推奨される。 |
A5052 | 非常に高い耐食性、良好な溶接性・曲げ加工性。中程度の強度。 | 一般機械用プレート、海洋環境部品、建築材料 | 加工性は良好だが、粘りがあるため切削条件の調整が重要。 |
A5056 | A5052よりさらに耐食性が向上、特に海水環境に強い。良好な溶接性。 | 海洋関連部品、船舶部品 | 丸棒での使用が多く、プレート材としての流通はA5052に比べて少ない傾向がある。 |
A6061 | 良好な加工性・耐食性・溶接性。強度と加工性のバランスが良い。 | 建築材料、自動車部品、半導体製造装置用プレート | T6処理(熱処理)により強度が向上するが、硬度も上がるため、工具選定や切削条件に配慮が必要。 |
A6063 | 良好な押出性、美しい表面仕上げ。 | 建築用サッシ、装飾品、ヒートシンク | 強度は比較的低いため、高負荷のかかるネジ部には不向きな場合がある。 |
A7075 | アルミ合金の中で最高の強度と硬度。 | 航空宇宙部品、高負荷構造用プレート | 加工性が他の合金に劣り、溶接も困難。切削抵抗が大きいため、剛性の高い設備と適切な工具が必要。 |
被削材の硬度がネジ切り加工に与える影響
アルミプレートの硬度は、ネジ切り加工の難易度や仕上がりに大きな影響を与えます。特に、高硬度材 (A7075、A2017など) の場合、以下のようなことが起きやすいため、適切な工具選定と加工条件の設定が不可欠です。
・工具への負荷増加:切削抵抗が大きくなり、工具の摩耗が早まります。
・振動(ビビり)の発生:加工中に振動が発生しやすく、ネジの精度や表面品位を損なう原因となります。
・加工精度の低下:工具のたわみなどにより、狙い通りの寸法が出にくくなることがあります。
2.下穴加工のポイント
ネジ切り・タップ加工の品質は、下穴加工の精度に大きく左右されます。アルミプレートへの下穴加工においては、以下のポイントを押さえることが重要です。
適切な下穴径の選定
下穴径の選定は、ネジの嵌合強度やタップの耐久性に直結します。その際、一般的にはJIS規格に基づいて下穴径を選定します。
一方、使用するタップ工具のメーカーが推奨する下穴径も重要な参考情報です。特定の材料や加工条件下で、工具寿命の延長や加工効率の向上を目的として設定されている場合があります。
基本的にはJIS規格を基準としつつ、必要に応じてメーカー推奨値を取り入れることで、より良い結果を得ることができます。
下穴加工時のドリル選定
アルミプレートの下穴加工に使用するドリルは、加工内容によって使い分けます。深穴加工や多数個の穴あけを行う場合は、加工効率と工具寿命の観点から超硬ドリルが有利です。一方、汎用性やコストを重視する場合はHSSドリル(ハイスドリル)が適しています。
ドリル種類 | メリット | デメリット | アルミプレート加工での主な用途 |
HSSドリル(ハイスドリル) | ・柔軟性があり、衝撃や振動に強く、欠けにくい ・比較的安価で汎用性が高い。 | ・耐摩耗性が低く、工具寿命が短い傾向がある。 ・高速切削や高精度加工には不向き。 | ・少量多品種のアルミプレート加工 ・一般的な穴あけ加工 |
超硬ドリル | ・高速切削が可能で、加工時間を短縮できる。 ・高精度な加工が可能で、良好な仕上げ面が得られる。 ・耐摩耗性に優れ、長寿命。 | ・HSSドリルに比べて高価。 ・靭性が低く、衝撃や振動に弱く、欠けやすい。 | ・大量生産時のアルミプレート加工 ・深穴加工 ・高精度な穴位置が求められる加工 |
さらに、平面度や平行度において0.01mm以下というような極めて高い精度が求められる場合には、切削加工の後に研削加工を施すことで、より精密な仕上がりを実現しています。当社では、協力工場との連携により、こうした高精度な要求にも対応可能な体制を整えております。
穴の位置精度とタップ立ての直進性確保
ネジ穴の品質を保証するためには、下穴の位置精度と、タップが真っ直ぐ入っていくための直進性の確保が極めて重要です。アルミプレート加工においては、以下の対策が有効です。
・センタードリルの使用:ドリル加工前にセンタードリル(またはNCスポットドリル)で位置決めを行うことで、ドリルの食い付きが安定し、穴の位置精度が向上します。
・ドリル加工後の追加工:より高い穴の位置精度や良好な内面粗さが求められる場合は、ドリル加工後にリーマ加工やエンドミルによるヘリカル加工を検討します。
・ネジゲージとピンゲージよる検査:加工後、ネジゲージとピンゲージを使用してネジ山の精度や有効径、直進性を確認します。ピンゲージによる下穴管理と、通りゲージと止まりゲージで正しく検査することが重要です。
・三次元測定器の使用:特に高い精度が要求されるタップ穴の位置や直進性については、三次元測定器による測定が推奨されます。
3.タップ工具の選定
アルミプレートへのネジ切り加工において、タップ工具の選定は加工効率、精度、そして工具寿命を左右する重要な要素です。代表的なタップの種類と特徴、そしてコーティングについて解説します。
タップ工具の種類と使い分け
タップ種類 | 特徴 | アルミプレート加工での主な用途 | 注意点 |
スパイラルタップ | ・溝がねじれており、切り屑を上(シャンク側)に排出する。 ・主に止まり穴の加工に使用される。 | アルミプレートの止まり穴加工全般。 | 切り屑の排出方向を考慮し、巻き付きによるトラブルに注意。切り屑によるプレート表面への傷にも注意が必要。 |
ポイントタップ (ガンタップ) | ・先端の食付き部に角度のついた溝があり、切り屑を進行方向(下)へ押し出す。 ・通り穴の加工に適している。 | アルミプレートの通り穴加工。 | 切り屑が下に排出されるため、治具やプレート下部に切り屑が溜まらないような配慮が必要。 |
転造タップ | ・切削ではなく、材料を塑性変形させてネジ山を盛り上げて成形する。 ・切り屑がほとんど出ない。 ・通り穴、止まり穴ともに使用可能。 | 延性のあるアルミ合金(A5052など)のプレート加工。切り屑を嫌うクリーンな環境や、ネジ強度を高めたい場合に有効。 | 下穴径の管理が非常にシビア。加工トルクが切削タップより大きくなる傾向がある。 |
スレッドミル (プラネットカッター) | ・マシニングセンタなどのNC工作機械で、ヘリカル補間機能を利用してネジを切削する。 ・1本で異なる径やピッチのネジ、右ネジ・左ネジの加工が可能(工具径による制約あり)。 ・切り屑処理が容易で、安定した加工が可能。 | 大径のネジ加工、深穴加工、硬度の高いアルミプレートへの加工、止まり穴の底まで完全ネジを切りたい場合などに有効。航空機部品用プレートなど。 | 専用のCAMとプログラムが必要。比較的高価な工具。 |
タップ工具のコーティング:性能向上と長寿命化の鍵
タップ工具の表面に施されるコーティングは、耐摩耗性、耐熱性、潤滑性を向上させ、工具寿命の延長や加工品質の安定化に貢献します。アルミプレート加工に適した代表的なコーティングを紹介します。
コーティング種類 | 特徴 | アルミプレート加工への有効性 |
TiN (窒化チタン) | ・金色の被膜。 ・耐摩耗性と耐熱性をバランス良く向上させる。 | 汎用性が高く、多くのアルミ合金プレート加工に適している。コストパフォーマンスに優れる。 |
CrN (窒化クロム) | ・摩擦係数が低く、潤滑性に優れる。 ・非鉄金属との親和性が低い(溶着しにくい)。 | アルミのような溶着しやすい材料のプレート加工に特に効果的。 |
その他特殊コーティング | 工具メーカー各社が、アルミ加工に特化した独自の多層コーティング(例:DLCコーティング、Vコーティング、Zコーティングなど)を開発しており、さらなる高性能化が図られている。 | メーカーの推奨に基づき、特定のアルミ合金プレートや加工条件に合わせて選定することで、最適な結果が期待できる。 |
切削タップ と 転造タップ(プレスタップ)の選択
アルミプレートへのネジ加工において、切削タップと転造タップのどちらを選択するかも重要な判断です。
切削タップ
切削タップは、材料を刃物で削り取ってネジ山を形成するため、切り屑が発生します。
・メリット: 比較的低い加工トルクで加工でき、多様な材質・硬度のアルミプレートに対応可能です。精度が高いネジ加工が可能です。
・デメリット:切り屑の排出管理が重要で、不適切な場合はタップの破損やネジ穴の品質低下を招きます。
転造タップ(プレスタップ)
転造タップ(プレスタップ)は、材料を塑性変形させてネジ山を盛り上げて成形するため、切り屑がほとんど発生しません。
・メリット:ネジ山の強度(特に引張強度やせん断強度)が切削に比べて向上します。切り屑が出ないため、クリーンな加工環境が保て、深穴加工でも切り屑詰まりの心配がありません。タップ寿命も一般的に長いです。
・デメリット:下穴径の精度管理が非常に重要です。切削タップに比べて加工トルクが高くなるため、機械の剛性やトルク能力が求められます。延性の低いアルミ合金(鋳物など)には不向きです。
選定のポイント
・切り屑を嫌う場合やネジ強度を重視する場合:延性のあるアルミプレート(A5052など)であれば転造タップが有利です。
・機械の剛性が低い、または加工トルクを抑えたい場合:切削タップが適しています。
・高硬度のアルミプレートや大径ネジ:切削タップやスレッドミルが適しています。特に大径ネジではスレッドミルが低トルクで調整しやすく有利です。
4.切削条件と加工方法
アルミプレートへのネジ切り・タップ加工において、適切な切削条件と加工方法の選択は、加工精度、工具寿命、そして生産性に大きく関わります。
回転速度の最適化:低速回転 vs 高速回転
タップ加工時の回転速度は、アルミプレートの材質、タップの種類、加工深さなどに応じて最適化する必要があります。
低速回転
■メリット
・硬度の高いアルミプレートや、深いネジ穴の加工に適しています。
・切削熱の発生を抑え、切削油が効果的に作用しやすいため、タップの摩耗を軽減し、工具寿命を延ばす傾向があります。
・加工状態を確認しながら慎重に進めたい場合に適しています。
■デメリット
・加工時間が長くなり、生産性が低下します。
・切り屑の排出性が悪くなり、特に止まり穴では切り屑詰まりのリスクが高まることがあります。
高速回転
■メリット
・加工時間が短縮され、生産性が向上します。量産加工や多数個のタップ加工を行うアルミプレートに適しています。
・切り屑の排出がスムーズになりやすく、加工面の仕上がりが向上することがあります。
■デメリット
・切削熱が高くなりやすく、切削油が十分に行き渡らない場合、タップの摩耗が早まり、工具寿命が短くなる可能性があります。
・高速回転に対応した高剛性の機械、高精度なホルダー、そして高性能なタップ工具が必要になります。
最適なクーラント(切削油)の選定
クーラント(切削油)の選定は、加工条件や目的に応じて適切なタイプを選ぶことが重要です。
クーラント種類 | 特徴 | プレート加工でのポイント |
エマルジョンタイプ | 水に希釈すると乳白色になる。 ・鉱物油の含有量が多く、潤滑性が比較的高い。 | 重切削や摩擦が多い加工、工具寿命を延ばしたいアルミプレート加工に適している。腐敗しやすいため、濃度管理やpH管理が重要。 |
ソルブルタイプ | ・水に希釈すると半透明または透明になる。 ・エマルジョンとソリューションの中間的な性質。 ・潤滑性と冷却性のバランスが良い。 | 軽切削から中切削、洗浄性も求められるアルミプレート加工に適している。 |
ソリューションタイプ | ・水に希釈すると透明になる。 ・油分をほとんど含まず、合成潤滑剤や界面活性剤が主成分。 ・冷却性と洗浄性に非常に優れる。 | 潤滑性は低いが、アルミは比較的柔らかいため、高速加工で冷却性を重視する場合や、加工後の洗浄性を高めたいアルミプレート加工で選択肢となることがある。ただし、タップ加工には潤滑性不足になることも。 |
5.ネジ山の強度確保
アルミプレートは軽量で加工性に優れる一方、材質が比較的柔らかいため、ネジ山の強度確保には注意が必要です。
アルミの柔らかさによるネジ山の摩耗・損傷リスク
アルミは延性が高く、硬度が低いため、摩擦や圧力によってネジ山が変形しやすい材質です。アルミ表面の酸化層が摩擦や圧力で破壊されると、基材が露出し、摩耗が進行します。また、アルミニウムの柔らかさにより、ネジ山が他の部品と接触して凝着(かじり)が発生しやすいです。
ネジ山強度を高める補強方法
アルミプレートのネジ山の強度を確保し、信頼性を向上させるための主な方法は以下の通りです。
・高強度アルミ合金の選定:A7075やA2017、A6061-T6などの高強度なアルミ合金を選定することで、ネジ山自体の耐摩耗性や耐荷重性を向上させることができます。
・陽極酸化処理(アルマイト処理):アルミプレート表面に硬質で耐摩耗性に優れた酸化皮膜を形成することで、ネジ山の耐摩耗性や耐食性を大幅に向上させることができます。ただし、皮膜の厚みによってはネジの嵌合がきつくなる場合があるため、処理前の下穴径やタップ加工の寸法管理に注意が必要です。皮膜が乗りすぎる処理には、オーバーサイズのタップを使用することも有効です。
・適切なトルク管理:ネジを締め付ける際は、トルクレンチなどを使用し、設計に基づいた適切なトルクで締め付けることが重要です。過剰な締め付けはネジ山の破損やプレートの変形を招きます。
・ヘリサート(ねじインサート)の使用:ステンレス鋼などの硬質なコイル状インサート(ヘリサート、エンザート、リコイルなど)をアルミプレートに挿入することで、強固なネジ山を形成します。
アルミ母材のネジ山に比べて大幅に強度と耐久性が向上し、繰り返し使用や高トルクでの締め付けが可能になります。
並目ネジ vs 細目ネジの選定基準
アルミプレートに使用するネジの種類(並目ネジか細目ネジか)は、用途や求められる特性によって選定します。
ネジ種類 | 特徴 | アルミプレートでの主な用途とポイント |
並目ネジ | ・ピッチ(ネジ山の間隔)が広く、一般的なネジ規格。 ・入手性が良く、作業性も高い。 | ・汎用的なアルミプレート部品の締結。 ・頻繁な取り付け・取り外しが想定される箇所。 ・作業効率を重視する場合。 |
細目ネジ | ・ピッチが細かく、ネジ山の接触面積が大きい。 ・並目ネジに比べて緩みにくい。 ・軸力が高い(同じ締め付けトルクでも高い締結力が得られる)。 ・微調整が可能。 | ・振動が多い環境で使用されるアルミプレート部品。 ・高い締結力や精密な位置調整が必要な箇所(例:精密機械のアルミプレート部品)。 ・薄板のアルミプレートで、ネジ山の数を増やして強度を確保したい場合。 |
選定のポイント
高い締め付け力や精密な調整が必要な場合、振動が多い環境では細目ネジが有利です。頻繁にねじを外す用途や作業効率を重視する場合、並目ネジが適しています。
6.タップ折れの防止策
タップ折れは、アルミプレート加工における最も避けたいトラブルの一つです。折れたタップの除去には多大な時間とコストがかかり、最悪の場合、加工中のアルミプレート自体が使用不可能になることもあります。
タップの食付き部の役割と重要性
タップの先端部分にある「食付き部」は、タップ折れを防ぐ上で非常に重要な役割を果たします。
・負荷分散:食付き部はテーパー状になっており、ネジ山を徐々に形成していくことで、タップにかかる切削抵抗を段階的に増加させ、急激な負荷がかかるのを防ぎます。
・案内部としての機能:下穴に対してタップを真っ直ぐに導き、安定したネジ切り加工を助けます。
・切り屑生成:食付き部で適切に切り屑が生成・排出されることで、加工中のトラブルを低減します。
スパイラルタップやポイントタップなど、タップの種類によって食付き部の形状や長さが異なり、それぞれ止まり穴用、通り穴用といった用途に適した設計になっています。アルミプレートの加工条件に合わせて、適切な食付き長さのタップを選定することが重要です。
タップ折れを防ぐための摩耗管理
タップの摩耗は、加工精度低下だけでなく、タップ折れの大きな原因となります。
摩耗の兆候
・加工中の異音(キーキー音など)、振動の増大。
・切削抵抗の増加(機械の負荷メーターで確認)。
・ネジ穴の仕上がり面の悪化(むしれ、バリなど)。
・ネジゲージ検査で、通りゲージが通りにくい、または止まりゲージが奥まで入ってしまうなどの寸法異常。
・切り屑の形状変化(細かくなる、色が変化するなど)。
摩耗管理の基準
・定期的な外観検査:タップの刃先の欠けや摩耗状態を目視や拡大鏡で確認します。
・加工穴数の管理:事前にテスト加工などを行い、アルミプレートの種類や加工条件に応じたタップの寿命(推奨加工穴数)を把握し、計画的に交換します。
・加工精度のモニタリング:定期的にネジゲージで加工されたネジ穴の精度を確認し、許容範囲から外れ始めたらタップの交換を検討します。
・トルクモニタリング:NC工作機械のトルク監視機能などを活用し、加工トルクが設定値を超えた場合にアラームを出すなどの対策も有効です。
タップが折れ込んでしまった場合の除去方法
万が一、アルミプレート加工中にタップが折れてしまった場合、以下の除去方法が考えられます。
放電加工
電極と折れたタップとの間にアーク放電を発生させ、タップを溶融・消耗させて除去する方法です。 母材であるアルミプレートへのダメージを最小限に抑えながら、高精度にタップを除去できます。硬度の高いタップでも除去可能です。一方で、 専用の放電加工機が必要であり、加工に時間がかかる場合があります。
特殊工具の使用
放電加工機に比べて手軽で、比較的安価に導入できます。事前に折れたタップの上面を平らに加工する必要がある場合もあります。
7.NC加工機でのネジ切り
アルミプレートにネジ切り加工を行う際、主軸回転と送り軸(Z軸)の同期制御が重要になります。この同期方法によって、使用するホルダーが異なります。
同期タップ(リジッドタップ)
主軸の回転とZ軸の送りをNCプログラムによって完全に同期させてネジを切る方法です。近年のマシニングセンタでは標準的な機能となっています。
■メリット
・高精度なネジ加工が可能で、ネジのピッチ誤差を最小限に抑えられます。
・高速でのタップ加工が可能となり、生産性が向上します。
・ネジ深さのばらつきが少なく、安定した加工が可能です。
・タップにかかる軸方向のスラスト負荷が軽減されるため、タップ寿命の延長も期待できます。
■デメリット
・機械側の同期精度が低い場合、逆にタップに過度な負荷がかかり、寿命低下やネジ精度の悪化を招く可能性があります。
・専用の同期タップ用ホルダー(リジッドチャック)が必要です。
フローティングタップホルダー
フローティングタップホルダーは、ホルダー内部に軸方向(伸縮)や径方向(フローティング)の「遊び」を持たせることで、機械の同期誤差や下穴位置の微小なズレを吸収する機構を持つホルダーです。
■メリット
・古い機械や同期機能がない、または同期精度が低い機械でも、比較的安定したタップ加工が可能です。
・下穴の位置ズレや、タップの芯ズレをある程度吸収し、タップの破損リスクを軽減します。
・機械への負荷を和らげる効果も期待できます。
■デメリット
・同期タップに比べて、加工速度を上げにくい傾向があります。
・フローティング機構により、厳密なネジ深さの管理や、高いネジ精度が求められる加工には不向きな場合があります。
・ホルダー自体の価格がリジッドチャックより高い場合があります。
選定のポイント
・高精度・高速加工を求める場合:機械に高精度な同期機能があれば、同期タップが第一選択となります。多くのアルミプレート加工で推奨されます。
・機械の同期機能に不安がある場合や、下穴精度にばらつきが予想される場合:フローティングタップホルダーの使用を検討します。これにより、タップの保護と安定した加工が期待できます。
・タップ径が小さい場合:小径タップは折れやすいため、機械の同期精度が十分でない場合はフローティングタップホルダーで負荷を逃がす方が安全な場合があります。
8.ネジの仕上げとタップ加工時の潤滑処理の重要性
アルミプレートへのタップ加工において、最後の仕上げや潤滑処理は、ネジの品質を左右し、工具寿命を延ばすために非常に重要です。特に、切削油剤だけでは対応が難しいような厳しい条件下では、追加の潤滑処理が効果を発揮します。
タップ加工時の補助的な潤滑剤
潤滑スプレー(タッピングスプレー、ペースト)
潤滑スプレーは、エアゾールタイプのスプレーやペースト状の潤滑剤で、タップや下穴に直接塗布して使用します。高い潤滑性能を持つものが多く、特に難削材や深い止まり穴加工で効果を発揮します。
■メリット
・切削抵抗を大幅に低減し、加工をスムーズにします。
・タップの摩耗を抑え、寿命を延ばします。
・むしれやカジリを防ぎ、美しいネジ山に仕上げます。
・アルミのような溶着しやすい材料のプレート加工に非常に有効です。
■使用時のポイント
・手軽に使用できますが、スプレータイプは飛散に注意し、作業環境の換気を十分に行ってください。
ペーストタイプは狙った箇所にピンポイントで塗布できますが、塗布に手間がかかる場合があります。
加工後、必要に応じて洗浄除去が必要になることがあります。
グリース塗布
グリース塗布は、ネジの組み立て時や、タップ加工後の防錆・潤滑目的で使用されることがあります。タップ加工そのものの潤滑剤として使用することは一般的ではありませんが、状況によっては補助的に用いられることもあります。
■メリット
・高い潤滑性と防錆効果が長期間持続します。
・スプレーに比べて飛散が少なく、作業環境を汚しにくいです。
■使用時のポイント
・タップ加工の直接的な潤滑としては、専用のタッピングペーストやスプレーの方が適しています。
・塗布に手間がかかり、過剰な塗布はゴミや異物の付着原因になることがあります。
選定のポイント
・難削性の高いアルミ合金プレートや、深穴タップ加工、小径タップ加工など、厳しい条件の場合:潤滑スプレーやタッピングペーストの使用が非常に効果的です。
・一般的なアルミプレート加工で、切削油剤の性能を補いたい場合:適宜、潤滑スプレーを併用することで、より安定した加工と工具寿命の延長が期待できます。
・作業性: 手軽さを重視するならスプレータイプ、ピンポイントで確実に塗布したいならペーストタイプが良いです。
アルミプレートの切削加工事例
A7075 プレート
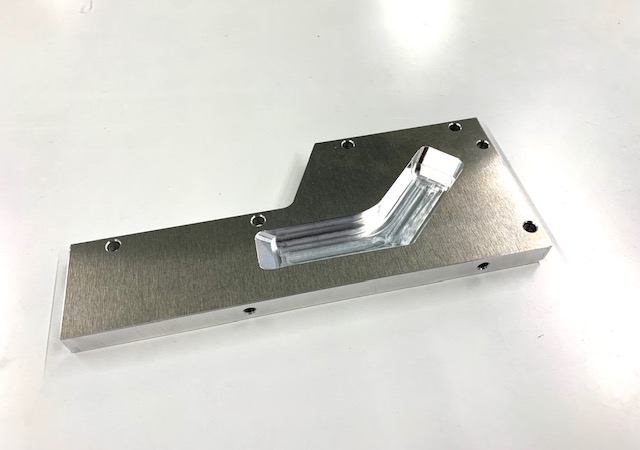
こちらは、医療機器向けのA7075アルミプレートです。従来は立形マシニングセンタで3工程を要していた本製品を、当社では横形マシニングセンタを活用し、2工程に集約。リードタイムを大幅に短縮し、生産性を向上させました。
高強度ゆえに歪みやすいA7075の特性に対しては、粗加工後に工具を変更し、仕上げ加工で歪みを最小化。厳しい品質基準にも対応しています。
A5052 ベースプレート
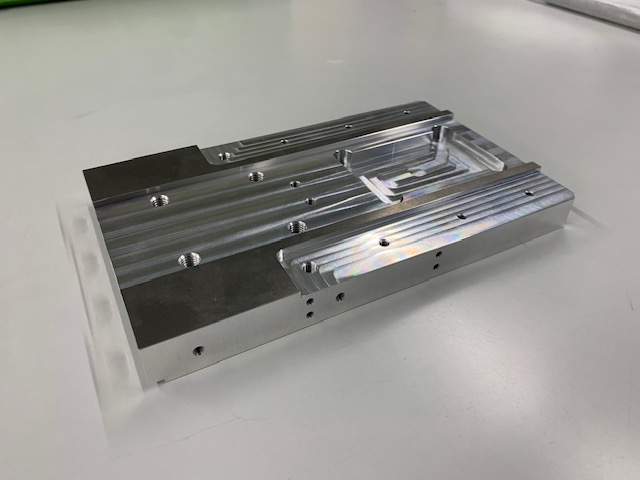
こちらは、半導体製造装置に使用されるA5052アルミ製ベースプレートです。裏面は立形マシニングセンタ「ニデックOKK VM53R」で、表面および側面4面は横形マシニングセンタ「牧野フライス a61-21PC」により一括加工しています。
工程を立形と横形で適切に分担・集約することで、安定した品質と高い生産性を両立しています。
アルミプレートのネジ切り・タップ加工なら、精密切削 スピード加工センター.comにお任せください!
当社では、長年にわたり培ってきた精密金属加工技術と豊富な経験を活かし、アルミプレートの加工を行っています。
アルミプレートへの高精度なネジ切り・タップ加工はもちろん、複雑形状加工や表面処理、小ロットから量産まで、まずはお気軽にご相談ください。
最後まで読んでいただきありがとうございました!
関連情報
- プレート切削加工
- アルミプレートの切削加工
- プレート加工におけるタップ深さorタップ位置の変更によるコストダウン
- プレートの切削加工における歪み対策
- プレート切削加工における立形・横形マシニングセンタの選定基準