シャフトの溝加工(キー溝・スリット溝・V溝・O溝・アリ溝加工)
シャフト部品に施される「溝加工」は、単なる形状加工にとどまらず、部品の性能・信頼性・長寿命を左右する重要な工程です。キー溝やスリット溝、V溝、Oリング溝、さらにはアリ溝など、その用途や目的に応じて求められる精度や機能は大きく異なります。
切削加工によるシャフトの溝加工では、工具選定や加工順序、治具設計などの最適化が欠かせません。また、ワイヤ放電加工とのハイブリッド活用によって、より複雑・高精度な形状への対応も可能となります。
本記事では、シャフトに施される各種溝加工の特徴や、注意点、実際の加工事例についてご紹介いたします。
シャフトにおける溝加工の種類
キー溝加工
キー溝加工は、シャフト(軸)とギアやプーリーといった回転部品を確実に結合し、トルクを効率よく伝達するために欠かせない加工です。シャフトの表面に規定の幅と深さで溝(キー溝)を切削し、そこにキーを挿入することで、軸と部品の一体化を図ります。
このキー溝は、JIS規格(例:JIS B1301)により、シャフト径に応じた標準サイズが定められており、設計段階での適合確認が重要です。
加工時に特に重視されるのが、キー溝の幅と深さの精度です。幅が広すぎればキーがガタついてトルクの伝達にムラが生じ、深さが浅ければキーが浮き、破損の原因になります。一方で深すぎるとキーが底付きしてしまい、肝心の側面での力の受け渡しが不十分となります。
キーの側面がシャフトとハブにしっかり密着することが安定したトルク伝達の要であり、キー溝加工における最も重要な加工ポイントです。
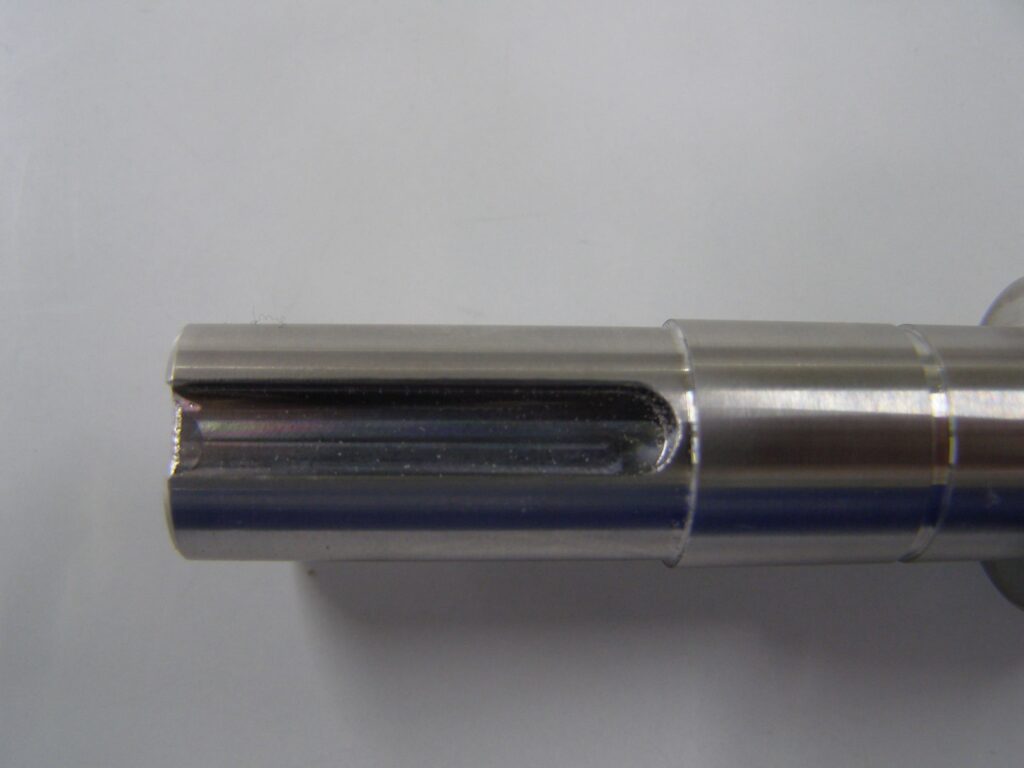
スリット溝加工
スリット溝加工(割りスリット)は、一見シンプルに見えるものの、その機能性は極めて高度です。トルクリミッターやクラッチのトルク調整機構、あるいはセンサーやエンコーダーでの位置決めなど、多岐にわたる用途があります。
この加工の特長は、溝の形状や配置によって回転精度・応答性に直接影響を及ぼす点にあります。とりわけ、半導体製造装置や精密測定機器といった分野では、スリットの寸法誤差が製品全体の性能に波及するほど、その精度が求められます。
加工時には、スリット幅の均一性、切り込み深さの精度、溝配置の対称性など、多角的な管理が必要です。最適な工具選定や加工条件の管理により、極めて微細な公差範囲を維持することが求められます。
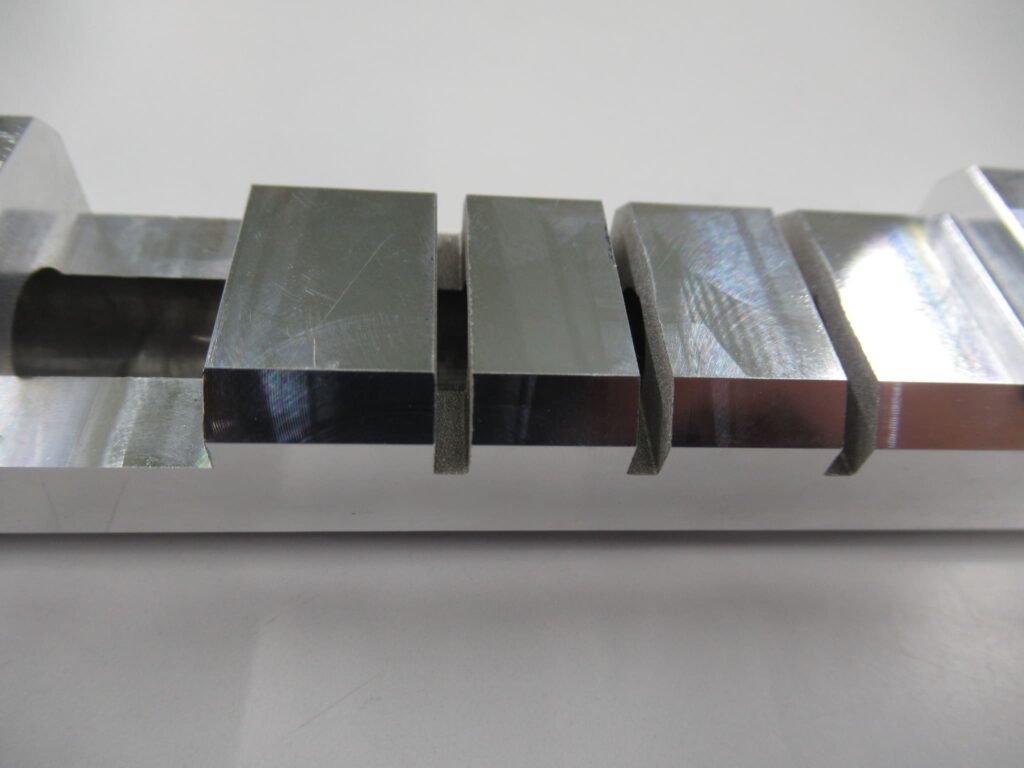
V溝加工
V溝加工は、Oリングや各種シール材の保持、部品の位置決め・センタリング、VベルトやVプーリーの嵌合部などに用いられる、機械構造の信頼性を支える加工です。
適切なV溝が設けられていなければ、ベルトが滑ったり、シール性が損なわれたりといったトラブルが発生しやすくなります。さらに、回転バランスや振動抑制といった要素にも関係し、V溝の品質は装置の長期安定稼働に大きく寄与します。
この加工においては、角度・深さ・位置の精度管理が極めて重要です。例えば角度にばらつきがあると、組立精度や曲げ加工時の仕上がりにムラが生じ、応力集中の原因となります。また、深さが不均一だと、Oリングの圧縮率に差が出て、密封性が低下します。位置ズレは嵌合部品との整合性を損ね、機能不良の要因になります。
そのため、V溝加工では工具の摩耗管理、加工プログラムの最適化、定期的な寸法確認といった工程管理が不可欠です。
Oリング溝加工
Oリング溝加工は、Oリングなどのシール材を保持し、気密性や水密性を確保するための重要な加工です。圧力容器、流体機器、真空装置など、漏れが致命的な影響を及ぼす機器において不可欠な構造であり、その品質は装置全体の信頼性を左右します。
加工時に特に重視されるのが、幅・深さの寸法精度に加えて、表面粗さの管理です。粗すぎればOリングとの接触面に隙間が生じ、リークの原因となります。一方で、鏡面仕上げのように滑らかすぎると、潤滑油が保持されずOリングが摩耗しやすくなります。
そのため、用途に応じた適度な表面粗さが必要とされ、仕上げにはホーニングやバニシングなどの表面処理が選ばれます。
アリ溝加工
アリ溝加工は、スライド機構や精密位置決め、さらにはOリングの保持構造としても用いられる高機能な溝構造です。その断面は台形(逆Y字型)で、部品同士を高精度かつ強固に嵌合させることができます。
この加工が特に重視されるのは、スライドテーブル、光学機器、真空チャック、治具プレートなど、高い再現性と剛性を必要とする機構です。わずかな角度ズレや寸法誤差が、摺動性や固定力に大きな影響を与えるため、ミクロン単位での精度管理が求められます。
真空装置では、Oリングを保持するためのアリ溝構造が使われることもあり、Oリングの脱落を防止しつつ、高い気密性を維持する複合的な機能部として重要です。
アリ溝加工には、専用のアリ溝カッターの選定が不可欠です。刃先角度と加工角度が一致していなければ、形状精度に狂いが生じ、嵌合性に支障をきたします。また、工具の摩耗による角度精度の劣化にも注意が必要です。
切削加工で溝加工をするメリット
設計変更にも即応可能
切削加工では、金型加工のような大掛かりな治具変更が不要です。CAD/CAM上でプログラムを修正すれば即座に加工対応が可能で、試作フェーズや多品種少量生産において大きな強みを発揮します。
材質や形状に応じた最適化が容易
アルミやステンレス(SUS)、樹脂、さらには多孔質材まで、切削加工は多様な材料に柔軟に対応します。加工条件(回転数、送り速度、切削油など)を適切に設定することで、高精度な溝加工が実現できます。
複合加工機による高精度な一貫加工
旋削・ミーリング・溝加工を1台の複合加工機で完結できるため、工程間のバラつきや段取り替えによる誤差を最小限に抑えられます。とくにシャフト部品では、ワンチャッキングで芯出し・外径加工・基準面加工を同時に行うことで、後工程との基準ズレを防止し、最終製品の精度向上につながります。
切削加工によるシャフトの溝加工の限界
切削加工は先述したようなメリットがある一方で、すべての溝形状や位置に対応できるわけではありません。溝の形状・位置・加工環境によっては、物理的な制約や加工精度の限界が存在します。
形状の限界
アンダーカット形状(T溝・アリ溝)
T溝やアリ溝のようなアンダーカット構造は、Tスロットカッターやアリ溝カッターなど専用工具を使うことで対応可能です。ただし、これらの加工にはいくつかの技術的な制約が伴います。
まず、加工時には工具の突き出し長さの制限が大きな壁になります。溝の奥行きが深い場合、長く突き出した工具を使用しなければならず、その結果、工具の剛性が低下しやすく、ビビリや加工精度の低下を招くリスクがあります。加えて、周囲の形状やワークの段差との干渉リスクも無視できません。加工ヘッドや工具がワークと接触しないようにするためには、事前のCAMシミュレーションや加工順の工夫、場合によっては治具設計の変更まで必要になることもあります。
内径溝(ボア内部のキー溝)
内径部に溝を加工する場合、スロッティングツールやブローチ加工が用いられます。中でも小径かつ深い溝は、加工スペースの制限や工具の曲がりによって、加工精度や再現性の確保が難しい領域です。
加工位置の限界
ワーク端面ギリギリの溝加工
ワークの端面に近い位置への溝加工は、クランプの干渉や工具の逃げ代不足により、非常に難易度が高くなります。加工時には最低でも2〜3mm程度の逃げ代を設計に盛り込むことが望まれます。
深穴内部や裏面の溝加工
裏面や深穴内部などの工具のアクセスが困難な箇所への溝加工は、通常のマシニングセンタでは対応が難しい場合があります。このようなケースでは
・専用治具の製作
・反転工程(ワークの再固定)
・複合加工機・5軸加工機による一発加工
などの対応策が必要となります。
切削による溝加工には確かに限界がありますが、工具の選定と管理、加工順序の最適化、治具設計の工夫、設備能力の把握と活用といった要素を総合的に工夫することで、一般的には困難とされる溝加工も高精度かつ安定して実現できる場合も多いです。
ワイヤ放電加工という選択肢
こうした切削加工の限界から、溝加工においてワイヤ放電加工を選択することもあります。ワイヤ放電加工は、ワークに直接接触せず、放電によって金属を溶融・除去する非接触加工であるため、以下のような利点があります。
加工バリが極めて少ない
非接触加工のため、「押し出し」や「めくれ」といったバリの発生源がほとんどありません。放電での微細除去により、シャープなエッジが得られ、バリ取り工程を省略できる場合もあります。
面粗さと形状精度に優れる
複数回の仕上げ加工を施すことで、Ra 1〜5μm程度の面粗度を実現可能。鏡面に近い滑らかな仕上がりが得られます。また、微細形状や鋭角形状の再現性に優れており、極細のスリットや直角コーナーのある形状も美しく仕上がります。
精密治具による位置決め精度
当社では、Vブロックや精密プレートなどの専用治具を自社製作しており、シャフトやワークを高精度に保持。溝加工時の位置ずれを防ぎ、寸法精度の高い仕上がりを実現します。
溝加工においてワイヤ放電加工の強みが活きる場面
こうした特長から、以下のような溝加工では、ワイヤ放電加工が有効です。
角部にRをつけたくない場合、または直角コーナーが必要な場合
一般的な切削加工では工具の形状上、どうしてもコーナーにRが残ってしまいますが、ワイヤーカットでは微細なワイヤー径により、極小Rでシャープな角を再現可能です。
極薄・極小のスリット溝
数mm以下のスリット幅でも、安定した精度で加工が可能です。微細な溝幅を求められる精密部品や電子部品などに最適です。
高硬度材・焼入れ材への加工
切削工具では対応が難しいHRC60以上の材質でも、非接触で加工できるため、焼入れ後の仕上げ加工などに力を発揮します。
工具が届かない内径溝や異形状への対応
ワイヤーは細長く、任意の形状に沿って動かせるため、内径部や入り組んだ形状の溝加工にも柔軟に対応します。
止まりのない貫通溝
ワイヤーカットは基本的に貫通加工を前提とするため、長尺や深溝でも形状精度・寸法精度の高い仕上がりが得られます。
ワイヤ放電加工の注意点
ただし、以下のような点には注意が必要です。
・止まり穴・止まり溝の加工は不可
・加工速度が遅い(一般的な切削に比べて1/50〜1/100程度)
- 例:厚み20mmで約5.5mm/min、100mmでは0.7mm/min程度
・完全な直角は不可(ワイヤー径の半分程度のRが角に残ります)
切削加工+放電加工のハイブリッド活用
溝加工における精度・コスト・加工性を高次元で両立させる手段として、切削加工とワイヤ放電加工を組み合わせたハイブリッド方式があります。例えば、複雑な形状や深穴がある溝形状であれば、放電加工を主体としつつ、工程前半では切削で荒加工を行うなど、切削を補助的に使う柔軟な工程設計が有効です。
また、放電加工は加工速度が遅く、電極の消耗も激しいため、切削と放電の加工時間・工具負荷のバランスを取ることが重要です。切削で荒加工を済ませ、仕上げのみ放電加工に任せるパターン、またはその逆に、ワイヤーカットで高硬度材の外形を抜いた後、切削で細部を整えるといった使い分けにより、総加工時間や工具・電極消耗の削減が可能になります。
ハイブリッド活用のメリット
微細・高硬度・複雑形状に強い
切削では難しい微細形状、高硬度材(HRC60以上)への対応や、直角コーナーなど工具径で制限される部位の加工は、放電加工で補完することが可能です。特に、ワイヤーカットは微細でシャープなスリット加工に向いており、高精度が求められる部品に最適です。
工具摩耗の抑制
放電加工は非接触方式であるため、切削と比べて工具の摩耗が大幅に少なくなります。たとえば、刃物の摩耗が激しい「抜き形状」の加工では、ワイヤーカットで外形を荒取りし、切削で仕上げだけ行うことで、工具寿命を延ばしつつ、加工コストも削減できます。
複雑形状への対応力
切削で大まかに加工した後、放電加工で微細部や深部を仕上げることで、複雑な輪郭形状や深溝の加工にも高い対応力を発揮します。特にアンダーカット形状や鋭角部などは、放電加工との併用でしか実現できないケースもあります。
同心度・真直度のズレ抑制
切削で加工した基準面や基準穴を、後工程であるワイヤーカット時のチャッキング基準として再利用することで、同心度や真直度のズレを抑制できます。複数工程にまたがる場合でも、基準の一貫性を保つことで、トータルでの精度が向上します。
ハイブリッド活用の注意点
加工時間の増加
放電加工は構造的に加工速度が非常に遅く、特に厚物ではさらに時間を要します。単純な形状で大量生産を行うケースでは、生産性の面でデメリットとなる可能性があります。
コスト増の可能性
加工効率を最適化すればコストダウンにつながる一方で、放電加工では電極の消耗、加工液の管理、放電機の稼働コストが無視できません。加工内容によってはコスト増加につながるケースもあるため、製品単価や求められる精度とのバランスを慎重に見極める必要があります。
シャフトの溝加工における精度管理と品質保証
高精度な溝加工を安定的に実現するためには、工作機械の性能や技能だけでなく、温度管理・加工順序・検査設備などを含む包括的な品質管理体制が不可欠です。当社では以下のような対策を行っております。
一定の温度環境下での加工
シャフトの長さや材質に応じて、加工応力や切削熱によるわずかな歪みや熱変位が発生します。特に、同心度や真直度が要求される溝加工では、こうした微細な変化が寸法誤差につながるリスクがあります。
当社では、空調設備を整えた恒温環境下での加工を徹底しており、外気温による機械やワークの寸法変動を最小限に抑えています。
高精度測定機器を活用した精度保証
当社では、高性能な三次元測定機や画像測定器を中心とした検査設備を多数導入しています。検査室は20℃±1℃に恒温管理されており、CNC三次元測定機を2台保有しています。主な測定設備は以下の通りです。
・三次元座標測定機(東京精密製 AXCEL)/測定範囲:X850 × Y1000 × Z600mm
⇒ 複雑な溝形状や大型部品の精密測定に対応。高剛性ボディと高精度プローブにより、微細な誤差も逃さず検出。
・画像寸法測定器(キーエンス製 IM-8030T)
⇒ 非接触・高速での測定が可能。量産品の一括検査や工程内品質保証の自動化に貢献。
・真円度測定機(ミツトヨ製 RA-2200 CNC)
⇒ シャフトや回転体における真円度・同軸度・同心度の精密評価が可能。回転精度が求められる溝加工に最適。
・ハンディプローブ型三次元測定器(キーエンス XM-T1200)
⇒ 現場での立ち会い検査や工程間測定に柔軟対応。短納期・多品種対応に威力を発揮。
ISO9001認証取得済み
品質マネジメントシステムに基づいた標準化された検査フローを構築。図面との照合・記録・報告までの一貫体制を整備しています。
一貫生産体制とトレーサビリティの確保
加工から検査、出荷まで一貫して社内で完結しています。製造履歴や測定結果も保存・管理され、万が一の追跡にも迅速な対応が可能です。
高信頼性分野への納入実績
半導体製造装置、医療機器、食品機器といった高い信頼性と清浄性が求められる分野でも多数の採用実績があります。
シャフトの溝加工事例
キー溝加工
本事例は、産業用制御機器向けの軸受けシャフトの加工です。キー溝加工およびキー溝底部の下穴加工を行うため、複合旋盤を用いてワンチャッキングで加工しました。全長160mmのシャフトに対し、各部の軸径精度5μm以内、同軸度0.03以内という高精度を実現しています。
スリット溝加工
本事例は、半導体製造装置に用いられるシャフトの加工です。複合旋盤でネジ切り・ブランク加工を行った後、マシニングセンタで側面穴あけ・複雑形状加工を実施しました。最終工程ではワイヤ放電加工機によるスリット溝加工を行い、重要な穴位置とスリット幅の高精度な位置関係を実現しています。
まとめ
当社では、豊富な実績とノウハウをもとに、お客様の図面の“その先”を見据えた加工提案を行っています。切削・放電・研削など多様な加工技術を組み合わせ、コスト・納期・精度の最適解を導き出します。
複雑形状や高精度部品に対しても、加工順序・治具設計・基準管理までを一貫して設計。複合加工機やワイヤーカットを駆使し、工程短縮と品質安定を両立します。社内に切削加工・放電加工・三次元測定を完備し、試作から量産まで一貫対応しています。外注レスによるリードタイム短縮と、トレーサビリティの確保で、安心とスピードを両立します。
当社での溝加工は、マシニングや複合加工機、ワイヤーカット放電加工機を保有しているため、より複雑な溝形状や深い溝形状にも対応可能です。図面上であきらめかけたような溝加工でも、一度ご相談ください。
最後までお読みいただきありがとうございました!